Five simple reasons for project failure in manufacturing industry
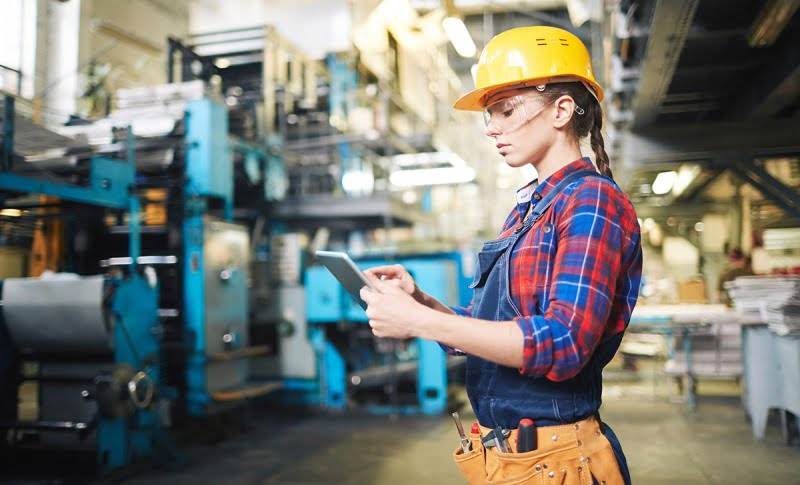
Manufacturing and engineering industry is an operation driven industry. It has set several standards in optimizing operations that are examples for other industries to adopt. However when it comes to projects, there is little focus and therefore projects execution in a manufacturing or engineering company often face delays, overrun and various other challenges.
I found five kay and also common issues that are causing these failures. The interesting point here is that these issues are so simple that any company can overcome them easily and prevent any project failure in future. Let’s us look at them.
Poor project management
Being an operation driven industry, it is quite obvious for a company try managing the project in the same way, they manage their operations. While projects are very different from operations and therefore need specific project management methodology to succeed. Poor planning, inability to steer project during execution and improper tools to measure project progress are few key issues that derail the projects. A meticulous plan and discipline execution is the kay to success. A poor planning results into unclear objectives, insufficient detailing of project plan, inefficient resource allocation and improper risk management. These issues lead to unclear direction to team members, ineffective resource utilization and getting caught unplanned for handling uncertain events during execution. When it comes to controlling, project managers are often handicapped by improper tools for measuring the project progress that make it hard for them to take right corrective measures to put the project back on track.
Depend on vendor for project management
Projects that are not core product development are often outsourced. For example expending an existing facility, building a new plant, implementing ERP etc. are often outsourced. If not fully, at least a large part. Though a plan is prepared in the beginning but that is too broad and grossly insufficient to execute and track the project. After the broad plan, the company or the project manager completely rely on vendor’s project management capabilities. In many cases, vendor itself does not have project management capabilities. Even so called Project Management Consultancies (PMCs) are basically construction management companies having construction technical knowhow but poor in project management. Even if vendors is expert in project management, it manages project at vendor’s side and does not coordinate among various departments on the buyer side. Thus the plan required by project manager for the work within company and integration of interdepartmental activities is normally missing. Therefore internal coordination, communication and integration remain an issues and significantly impact the project progress.
Low awareness about project management and its benefits
I see a lot of people think that project management means PERT/CPM. Probably it is because PERT/CPM is what is taught in industrial management in the name of project management. Many people think project management means using a tool like MS Project or Primavera. With this limited understanding, it is quite apparent that a holistic approach to project management is missing which in turn lead to delays, cost overruns and quality issues in the projects. While on one side companies strive to use tools like Lean, Six Sigma etc. to achieve excellence in operations, hardly any efforts is taken to implement project management principles, tools and techniques to improve project deliveries. Some companies realize the issues in projects but try to use tools and techniques that are fit for operations and not for projects. It is because these are the tools and techniques that they know.
It is not for me
This will not work here. We don’t execute projects like this. Our projects are different. You don’t know working style here. We tried earlier but did not succeed. This is something not specific to manufacturing industry but exist in almost all industries. A systematic way of executing projects often face resistance. These resistances are mainly due to fear of moving out of comfort zone as it discipline the people and take away their freedom to do anything anytime. It may be because of some failure to implement project management practices earlier. But the biggest reason is we have more than 8 hours of work in hand, where is the time to take a new initiative?
It is always a chicken and egg story. Because our hands are overflowing, there is no time for adopting project management practices and until we take such initiatives, our hands will continue overflowing. The only way to get out of this downward spiral is to hold on, apply best practices in project management to deliver more in less time and thereby always having time for continuously strengthening it.
Absence of a guide/advisor on project management
This problem is normally faced by self-aware people who understand that they have to implement project management principles. They go them-self and send their people for training to learn new skills in project management and implement them in the company. The challenges here is that a training does not make a person master of the subject. When people go to implement what they have learned in the training, they face real life issues and challenges which may not be easy to resolve due to lack of experience in implementing project management practices. A project management guide/mentor/consultant could be of immense use here as he will fill this gap. He can guide the team and help it to overcome the challenges and make project to succeed. Taking such initiatives without any guide/coach/mentor in general cause early failures or prolong the success that may demotivate the team.
As I stated in the beginning, these issues are simple and easy to overcome if one decides to get them away. A three way approach will be very useful in delivering successful projects in a manufacturing company. First, adopt a project management methodology and standardize it for every project to follow. Second, give regular trainings to people involved in the project (not just to project managers only) by a project management expert on the methodology adopted and third, have a project management coach/mentor to guide and support project team so that team can resolve issues and overcome challenges to take the project to success.
I look forward for your views.
Your findings are absolutely correct. Also the suggested solution is a really workable option. Only one change I would suggest that a mentor must exist inside the company. He should be a person with mandate by top management, to implement project management methodology. Long back I had witnessed such a scenario, where IT processes were implemented as a project with a very senior IT manager was sent as Project manager reporting to plant head & then IT department got due respect in that Organization.
I understand your point and agree that one cannot succeed without top management support however I believe mentor can be from outside of the organization also. If the mentor has support of top management and work closely with team, I see every reason to succeed irrespective of mentor is from outside or inside. We have wrote success stories by providing interventions.
I agree with your observation with IT department.